Flexible PCB Circuit Materials

With the rapid and continuous development of electronic products, the field of electronic assembly technology faces severe challenges one after another. To keep pace with advancements in electronic technology, bold innovations have been made in electronic assembly. Against this backdrop, flexible PCB circuits emerged—featuring delicate conductive traces and manufactured from thin, compliant polymer films. These circuits are compatible with surface mount technology (SMT) and can be bent into countless desired shapes.
Flexible PCB circuits using SMT technology can be extremely thin and compact, with insulation thicknesses less than 25μm. They can be freely bent or even rolled into cylindrical forms to maximize three-dimensional space utilization. This breaks the traditional mindset of focusing solely on planar area, enabling efficient use of volumetric shapes. As a result, they significantly enhance the effective usage density of conductive traces per unit area, achieving high-density assembly.
In recent years, flexible PCB circuits have expanded into applications such as radio communications, computers, and automotive electronics. Originally used exclusively as substitutes for rigid cables, they now serve as mature alternatives to rigid circuits and PCBs in scenarios requiring thin or three-dimensional circuitry. To meet hybrid rigid-flex requirements, rigid-flex technology integrates flexible PCB circuits with rigid circuit boards.
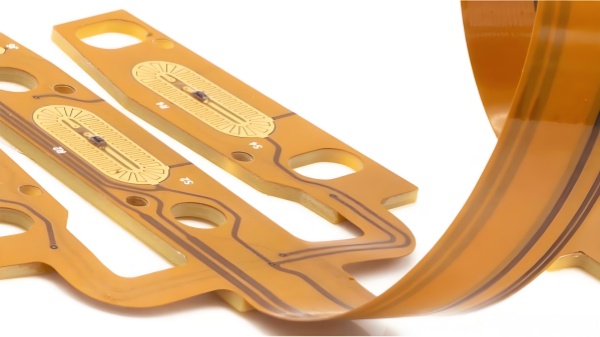
1. Early Applications of Flexible PCB Circuits
Although flexible PCB circuits with SMT technology represent modern high-tech, they build on the fundamental principles of the earliest printed circuit traces, tracing back to the 1970s. One of the first practical uses of SMT flexible PCB technology occurred in the early 1970s when Texas Instruments developed calculators. Dual in-line package (DIP) integrated circuits were placed into gull-wing components and heat-sealed onto flexible PCBs with heat bars. The base film was heat-sensitive polyester, manufactured via continuous roll pressing for circuit fabrication. Another early example was Polaroid cameras in the early 1980s, which used polyester-based flexible PCBs soldered via wave soldering. Since the 1980s, the combination of flexible PCBs and SMT has thrived. Once manufacturers recognized SMT as ideal for film substrates, many quickly adopted the technology.
2. Key Materials in Flexible PCB Circuits
The primary materials in flexible PCBs are insulating films, adhesives, and conductive traces. Insulating films form the circuit base. Adhesives bond copper foil to the films, and in multi-layer designs, internal layers are laminated together. Protective coatings isolate circuitry from dust, moisture, and reduce stress during flexing. Conductive layers are provided by copper foil.
Some flexible PCBs use aluminum or stainless steel as stiffeners to ensure dimensional stability, provide mechanical support for component/connector insertion, and relieve stress. Stiffeners are adhesively bonded to the circuit. Another material is bond ply, an insulating film with adhesive on both sides, offering environmental protection, electrical insulation, and lamination in low-layer count multi-circuits.
Common insulating films include polyimide and polyester (PET). In the U.S., ~80% of flexible
PCB manufacturers use polyimide films, while ~20% incorporate polyester. Polyimide is
non-flammable, dimensionally stable, tear-resistant, and withstands high soldering
temperatures. Polyester (PET) has similar physical properties, lower dielectric constant,
and minimal moisture absorption but poor heat resistance. With a melting point of 250°C and
glass transition temperature (Tg) of 80°C, PET is limited in high-soldering applications but
suitable for phones and other non-harsh environment devices.
Polyimide films are typically paired with polyimide or acrylic adhesives; polyester films with polyester adhesives. After soldering or lamination, bonded materials offer stable dimensions. Key adhesive properties include low dielectric constant, high insulation resistance, high Tg, and low hygroscopicity.
Beyond laminating insulators and conductors, adhesives serve as protective coatings (coverlays or surface coatings). The difference lies in application: coverlays are laminated over circuit layers, while surface coatings are screen-printed.
Adhesive-less laminates offer thinner profiles, better flexibility, and thermal conductivity compared to adhesive-based structures. Their thinness and heat-resistant design allow use in scenarios unsuitable for adhesive-based materials.
Copper foil in flexible PCBs is produced via electrodeposition or forging. Electrodeposited foil has a glossy and matte side, forming bendable materials in various thicknesses and widths; the matte side often requires treatment for adhesion. Forged foil is bendable yet rigid with smooth surfaces, suitable for dynamic flex applications.
3. Lamination Structures and Characteristics of Flexible PCBs
Material suppliers like DuPont, ICI Americas, Rogers, and Sheldahl offer specialized lamination structures for niche applications. DuPont provides polyimide-acrylic structures and various polyimide laminates. Its Kapton® polyimide film is the base for Pyralux® products, including FR (flame-retardant) and LF copper-clad laminates, bond plies, and coverlays. Pyralux AP laminates also use Kapton film.
Pyralux FR copper-clad laminates consist of Kapton film with single/double-sided copper foil bonded via proprietary flame-retardant Class C acrylic adhesive. Pyralux FR bond plies have Class B acrylic adhesive on both sides of Kapton film; coverlays have Class B adhesive on one side. The LF series is non-flame-retardant but otherwise comparable to FR.
Pyralux PC is a photoimageable coverlay made of acrylic, urethane, and thioimide, suitable for radio, computer, industrial, and medical devices requiring repeated flexing (not extreme dynamics).
Pyralux AP is an adhesive-less, double-sided copper-clad laminate of Kapton film and copper foil, thermally stable up to 200°C+.
Rogers Corporation (Chandler, AZ) uses Kapton film as the base for its R/flex 2005 flame-retardant series, including Kapton-based coverlays, bond films, and copper-clad laminates with flame-retardant adhesives. Rogers also offers adhesive-less flex-imid 3000, a copper-clad polyimide laminate rated for continuous operation at 160°C.
PEN (polyethylene naphthalate)-based insulating films (e.g., ICI Americas’ Kaladex) resemble polyester but offer superior thermal performance, with a Tg 120°C higher than PET. PEN’s dimensional stability and chemical resistance make it a substitute for polyester and polyimide in specific applications.
Sheldahl (Northfield, MN) manufactures adhesive-less flexible PCB materials under its Novaclad and Novaflex lines. Novaclad is a copper-clad polyimide available in custom foil thicknesses and properties. Novaclad G2200 copper-clad laminates excel in chemical and heat resistance, tested for 1000 hours at >150°C.
Novaclad G2300 laminates pass long-term thermal aging at 150°C for 1000 hours. The G2400 MCM-grade material targets multichip modules (MCMs) and chip scale packages (CSPs), enabling laser-drilled microvias without fillers, fine-line imaging for thin copper foil, and enhanced chemical resistance for noble metal coatings (e.g., Pd, electroless Ni/Au). Its smooth film-foil interface improves high-speed signal integrity.
Sheldahl’s Novaclad uses proprietary vacuum metallization to deposit ultra-thin pure copper layers on polyimide films, which are then electroplated to target thicknesses. These serve as the base for adhesive-less Novaflex circuits, overlaid with Novaflex insulating coverlays after circuit imaging. Designed for harsh environments, Novaflex offers superior flexibility, chemical resistance, high-temperature performance, and thermal dissipation.
4. Polymer-Additive Flexible PCB Technology
U.S.-based Poly-Flex Circuits has developed a unique flexible PCB technology. Instead of copper foil and adhesives, it uses silver particle-filled conductive ink printed on polyester insulating films. A conductive epoxy (Poly-Solder) bonds surface mount devices to the circuitry.
Multi-layer circuits are formed by printing a polymer-based insulating layer over the first conductive layer, followed by a second conductive layer. Interconnections between layers are achieved via conductive vias.
Suitable for -40°C to 85°C applications, this technology replaces standard flexible PCBs in products like telephones, keyboards, thermostats, gaming consoles, information displays, and medical devices.
5. Conclusion
While the material choices for flexible PCBs are somewhat constrained, they generally meet requirements across most electronic applications. Flexible PCB materials will continue to play a critical role in radio communications, computers, medical, industrial, and automotive electronics.